How To Do Takeoffs From Blueprints?
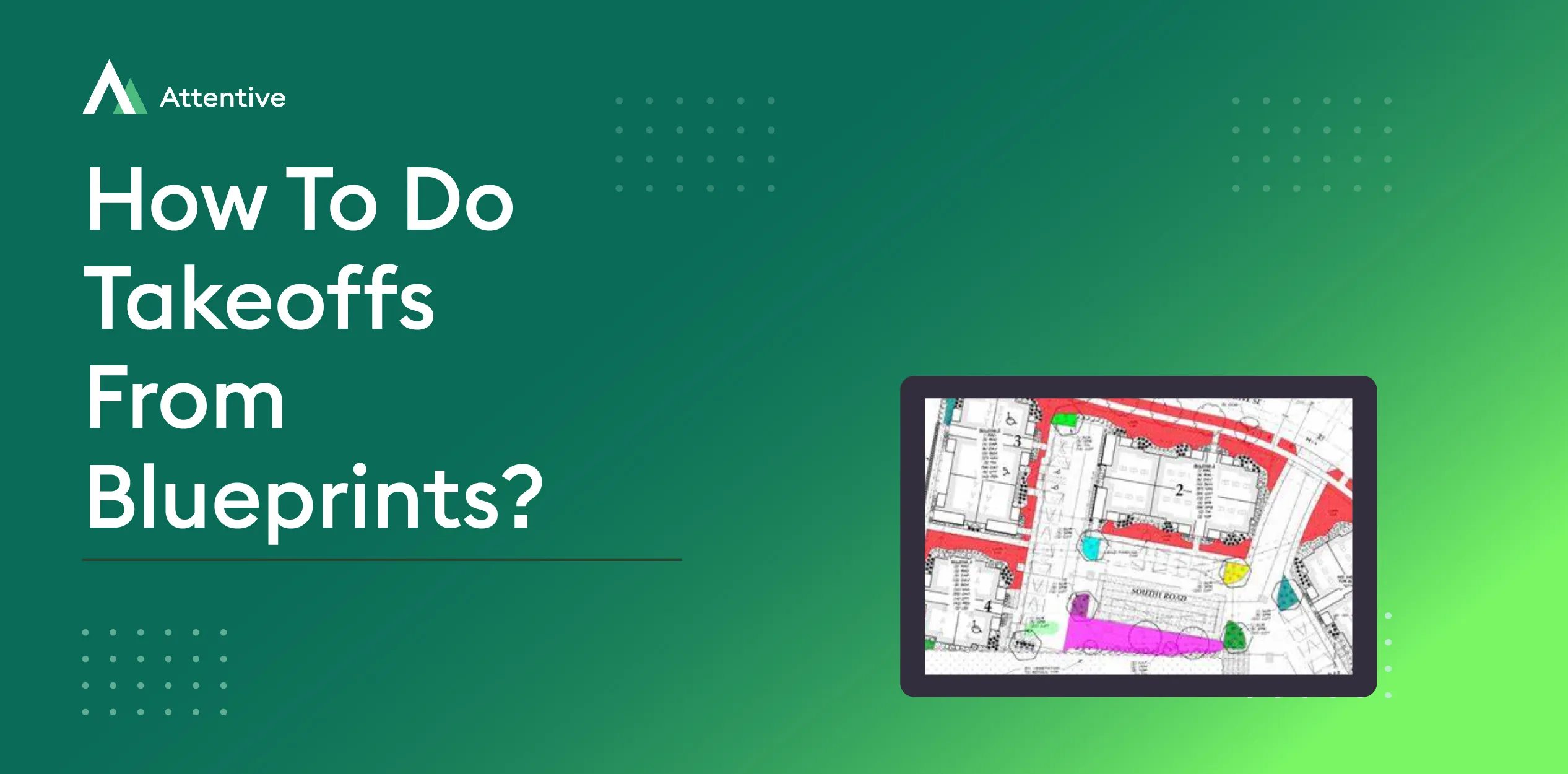
Table of content
Subscribe to get updates from Attentive!
How to do takeoffs from blueprints? All your queries are answered. But first, a question for you- did you know that for every five jobs you bid on, you seal the deal for one of them? Yes! Hence, as a contractor or subcontractor, you must master the bidding process.
And, to submit a successful bid- you need a clear idea of the different types and quantities of materials needed to finish a construction project. In addition to providing an idea of the labor expenses related to the installation or building of the materials, accurate takeoffs guarantee that the costs and material requirements are properly estimated. Construction takeoff, material takeoff (MTO), or just takeoff are all terms used to describe this. It is a crucial step in the estimation process for a construction project.
Experienced builders typically estimate materials for smaller jobs via guesstimating. But they aren’t necessarily accurate. Besides, larger projects require a more thorough procedure. It gives your client a very precise estimate of the expenses, equipment, labor, and materials.
So, what is a takeoff in construction? And what exactly is included in a blueprint takeoff? How to do takeoffs from blueprints? How doing takeoffs from blueprints manually bottlenecks the sales process? Are there any benefits of getting automated blueprint takeoffs? In this blog, we answer all of these questions. Read on.
So here’s a deep dive into how to do takeoffs from blueprints you didn’t know you need.
What are the takeoffs from blueprints in construction?
Construction takeoffs, also known as material takeoffs, are a crucial component of virtually any construction project. Here, no matter the scale of the task, takeoffs are absolutely essential to giving the builder, trader, or end consumer an exact quote.
A takeoff consists of a list of every material that will likely be used in the project. This allows for the estimation of the number, length, volume, and weight of the items as well as the project’s estimated completion time. And determining the necessary material quantities for the project is an essential step in the takeoff process.
Thus, here are the 9 main components of a construction takeoff.
- Labor
- Material expenses
- Equipment
- Administration costs
- Subcontractor costs
- Overhead costs
- Contingency
- Indirect costs
- Markup or profit
Labor
Labor costs encompass the wages or salaries of the workers involved in the construction project, including skilled tradespeople, construction workers, supervisors, and project managers.
Additionally, you must know the number of workers you need for each task on each day. That allows you visibility into what you’ll spend on them.
Material expenses
Here, the material expenses refer to the cost of all the materials required for the construction project, such as concrete, steel, lumber, plumbing fixtures, and electrical components.
Equipment
Your equipment costs involve the expenses associated with renting, purchasing, or operating construction equipment and machinery required for the project, such as excavators, cranes, bulldozers, and power tools.
Ascertain the type of construction equipment needed on the basis of the work to be done and outline the renting, purchasing, or operating costs.
Administration costs (procurement and site supervision)
Administration costs include expenses related to project management, procurement of materials, site supervision, and coordination. Particularly, you also consider ensuring smooth workflow and adherence to timelines and quality standards.
Subcontractor costs
This involves estimating the costs associated with subcontracted work or specialized services you may need for the project.
In essence, make a note of the specialized services required for the project to decide on the subcontractor costs.
Overhead costs
Yes, you guessed it. Overhead expenses comprise project management fees, insurance, permits, and general administrative costs. These are factored into the takeoff to ensure all necessary expenses are accounted for.
Contingency
Construction businesses usually add a contingency amount to the takeoff.
Your contingency could cover anything from covering accident costs to equipment breakdown costs.
This amount accounts for:
- Unforeseen circumstances like extreme weather conditions, labor strikes, etc.
- Changes in scope or project requirements
- Beyond control, unexpected site conditions like unstable soil, hidden utilities, or hazardous materials
- Potential safety risks that may arise during the construction process
- Equipment or machinery breakdown
Indirect costs
Indirect costs, as the name suggests, can include expenses indirectly associated with the project. Then this can range from utilities, temporary facilities, and site security to environmental compliance.
Markup or profit
The construction markup is the extra amount added to the direct costs of a construction project to determine the total selling price. As a result, the markup allows the construction company or contractor to cover their expenses and make a profit.
To clarify, a markup or profit margin gets added to the total estimated costs accounting for the company’s desired profit on the project.
The specific percentage of the markup can vary depending on factors like the type of project, market conditions, competition, and the contractor’s business model. In effect, the markup aims to ensure that the construction company or contractor can cover all their costs and make a reasonable profit.
What is the difference between takeoffs from blueprints and estimates?
Takeoff involves determining the quantities or materials required for a project. It focuses on establishing the amount needed. On the other hand, estimating involves calculating the sourcing cost of materials. Here, you multiply unit costs by quantity. And, you consider the required man-hours and equipment. Naturally, the next step is transforming the estimate into a proposal for the project.
Let’s understand this with a commercial construction project example. An MNC wants to erect a new office building.
Takeoff
The estimator, when doing construction takeoff, will meticulously analyze the blueprints and determines the quantities of various materials required, such as steel beams, concrete slabs, and ceiling tiles, based on the project’s specifications.
Estimate
On the other hand, during the estimating phase, the team assigns costs to these quantities. This will include accounting for labor expenses, equipment rentals, subcontractor fees, and administrative costs like procurement and site supervision.
In a nutshell, the estimate provides a detailed breakdown of all the expenses involved in the project, enabling accurate budgeting and informed decision-making.
Who does the takeoffs from blueprints?
The construction takeoff is frequently created by an estimator. However, in smaller companies without an estimating team, the business owner or the business development manager dons many hats and doubles up as the estimator. Every component needs to be included, and the person in charge of the construction takeoff must make sure of this.
Even individuals working in the electrical, roofing, plumbing, painting, flooring, drywall, and concrete industry rely on takeoffs to estimate the amounts and types of material needed for particular projects.
And- the landscaping maintenance and construction industry nowadays offer very little room for error. Estimators must make sure that project expenses and materials are correctly estimated in order to generate precise estimates and optimize their bids in light of escalating material costs and razor-thin margins.
How do general contractors and estimating professionals place a competitive bid?
Let’s understand how general contractors and estimating professionals develop a comprehensive and competitive bid. A bid that aligns with the project requirements and maximizes your business’s chances of winning the contract because a competitive bid provides the best quality at the most affordable cost.
Contractors usually develop a competitive offer by:
- Analyzing the project requirements and bill of numbers
- Conducting material takeoffs
- Reviewing project plans and specifications
- Conducting site visits
- Requesting and analyzing subcontractor quotes
- Evaluating labor requirements
- Factoring in overhead costs
- Determining profit margins
- Incorporating contingency and risk factors
- Reviewing historical data
- Considering market competitiveness while ensuring profitability
- Presenting a professional and compelling bid proposal
How is preparing a bid different from pricing construction jobs?
Preparing a competitive construction bid involves analyzing the project requirements, understanding the scope of work, and determining the resources needed to complete the project.
Here, your team also evaluates the costs associated with labor, materials, subcontractors, and overhead expenses. Likewise, your focus remains on creating a comprehensive and competitive proposal that aligns with the client’s budget and expectations.
On the other hand, pricing construction projects specifically focuses on calculating the cost of a specific project. Calculated costs are based on the estimated quantities of materials, labor hours, equipment usage, and other direct costs. Again, it involves determining the unit costs for materials, labor rates, and overhead expenses and applying them to the project’s specifications and requirements.
Additional Read: Pricing Construction Projects: Best Practices
If you think about it, the pricing process aims to arrive at an accurate and profitable cost for the construction job.
How to do takeoffs from blueprints accurately?
On a high level, there are 3 sections that we can divide doing blueprint takeoffs:
Manually tracing blueprints
- Use physical measurement tools like rulers and scales to measure dimensions and quantities directly from the blueprints.
- Take caution to ensure precise measurements and avoid human errors.
- A time-consuming process that requires careful attention to detail.
- Restricts estimators to spend their time only on takeoffs
Digital takeoff tools (endless clicking)
- Utilize specialized software that allows users to click on individual items or areas on the digital blueprint to measure quantities.
- The software calculates the measurements based on the clicked areas and provides a total quantity.
- Besides being faster than manual tracing, but still relies on manual effort and may have limitations in accuracy.
Automated takeoffs from blueprints
- Use AI-based takeoff solutions designed for automated takeoffs from blueprints.
- Upload the blueprint into the software and define the scope of work.
- The software utilizes advanced algorithms to automatically extract dimensions, quantities, and other relevant data.
- Provides more accurate and efficient takeoffs, minimizing human errors and saving time.
Problems with manually doing takeoffs from blueprints
Traditionally, material estimates have been made by hand. By utilizing blueprints to determine how much material—such as bricks, steel girder, piping, etc.,—will be required to finish the project.
These manual takeoffs frequently entail measuring a blueprint to obtain the necessary measurements. However, it is still possible to make a measurement error even on relatively smaller sites.
But for the type of work being quantified, it is essential that the estimator can precisely decode blueprints and drawings (general building plans, electrical and plumbing schematics, etc.). Finally, these will have diagrammatic representations of the project’s dimensions and numerous symbols and comments that might specify the materials needed.
Here’s what a construction plan looks like when you are manually tracing a blueprint
You can use colored pencils, inks, or markers to separate the various objects and kinds of material mentioned in these blueprints. Now, calculating the volume of material needed is necessary for items like concrete or asphalt.
Here, the required area would be included in the materials used over a sizable region, which would be required for flooring or tiling materials. In addition, a straightforward count is sufficient in some circumstances. This would apply to manufactured things like light fixtures.
Moreover, the materials must now be given a price after the estimator has extracted all of the items required for the project and determined the quantity associated with each one. The next step in how to do takeoffs from blueprints is to figure out how much each item on your list will cost. You may have to rely on your knowledge of the industry at this point to estimate the cost of the materials.
In a nutshell-
- Commercial landscaping and paving construction projects often involve intricate blueprints with various layers of information, including site plans, grading plans, irrigation plans, planting plans, and hardscape details.
- Extracting measurements manually from these blueprints is time-consuming and prone to errors.
- Complex or poorly labeled blueprints can make it difficult to accurately understand the design intent and specifications.
- Finally, misinterpretation or omission of important details from the blueprints can lead to inaccurate takeoffs and potential issues during project execution.
Why do you need accurate takeoffs from blueprints?
Inaccurate takeoffs can bottleneck the sales process. Because, today, “bids” close faster than ever. You have the BD or an estimator with a lot of work. Next, they simply take the designs and calculate a price in their head without caring if the price is high or not since they are already booked solid. There are 2 ways this usually happens:
- Low Bidder
- High Bidder
Low Bidder
You have the “low bidder,” who undertakes a little more research into the materials needed. Then, they prepare estimates of the labor hours needed to complete the work, typically based on prior experiences.
High Bidder
Or you have the high bidder. Without precise or nearly precise measurements, it’s likely that you’ll get too little or too much of the material. Additionally, you overbid or underbid on labor, supplies, and other costs. Further, incorrect estimates result in placing an unsuccessful bid.
That’s why you need accurate takeoffs from blueprints
Hence, it is essential to get accurate estimates so that you get the right margins, schedule your operations well, and have a winning bid. Here, the estimate serves as the foundation for your budget, which most likely includes charges for various construction-related expenses like materials and permits. You can stick to your budget and know where your money is going if you have a precise estimate.
Additionally, a construction estimate enables you to give consumers more precise estimates of the potential cost of a project. And customers often prefer to have precise quote ranges so they can estimate their likely project costs. A thorough construction estimate can help you focus your proposal range and gain more clients.
Benefits of getting automated takeoffs from blueprints
Manual takeoffs have been traditionally used to prepare estimates. But they can be labor and time intensive. And if you measure, calculate, or count incorrectly, it can lead to erroneous estimates. An inaccurate takeoff can negatively impact the daily workflow, budget, timeframe, and ultimate cost estimation. A successful operation depends on doing it correctly.
Many estimators are choosing automated takeoff over traditional ones as they are able to save time while getting greater accuracy. Besides, contractors are able to bid more, especially during the busy seasons. Equally important, the construction takeoff software allows you to upload blueprints and get accurate measurements.
Increasingly, automation has sped up the process and delivered better accuracy. You can upload plans to takeoff construction software, such as Attentive.ai, for blueprint takeoffs, allowing the user to get takeoffs more easily.
How to get automated takeoffs from blueprints with Attentive.ai?
If you’re looking for a 5-6 step process, you might be in for a disappointment because, with Attentive.ai, you can get accurate, hyper-detailed blueprint takeoffs in 3 steps only.
Step 1: Upload blueprint plans.
Step 2: Define the scope of work
Step 3: Hit proceed to get takeoffs.
Once you sign up on Attentive.ai’s AutoMeasure platform, switch to the blueprint takeoff mode. Here, you simply scan the blueprint into the software for a digital takeoff. Once the layout has been thoroughly examined, the platform creates a detailed list of every material needed for the project.
Here’s what automated paving construction takeoffs from blueprints look like with Attentive.ai
Wherever necessary, the estimator can always make manual revisions. The materials can then be given automated, error-free formulas and processed through the software to provide precise construction takeoffs.
But that’s not it! Enjoy fast turnaround on your takeoffs, queue multiple blueprint plans, and free up your estimator’s bandwidth. In any event, they can focus on reviewing cost estimates, value engineering, and scoping.
An example of getting takeoffs from blueprints with Attentive.ai
Imagine you have to construct a pool. So, here’s how you will start it. Most probably, you’ll give the project to a landscape architect. They will design the landscape while deciding where you’ll erect the main structure and have sofas, pool chairs, tables, other furnishings, hedges, shrubs, etc. This way, they will prepare a blueprint for you that may look like this.
Coupled with this process, a construction company can create the main structure. A pavement maintenance company will take care of the pavement, parking lot areas, driveways, etc. And a landscaping company will handle the landscaping elements, including softscapes such as installing evergreen flowers, shrubs, etc.
Here’s how Attentive.ai’s Automated Takeoffs From Blueprints Finally Look.
Now, the landscaper in charge of counting, measuring, and calculating elements can log in to the Attentive.ai software and upload the blueprint. This way, you can get accurate takeoffs of all the designated areas, the number of furnishings, quantity, and type of materials, type of fabric, finish, equipment, labor, etc.
What kind of construction jobs can you get takeoffs from blueprints for with Attentive.ai?
So, with our blueprint takeoff software, you can get takeoffs for the following types of construction jobs:
- Landscaping
- Paving
- Masonry
- Mechanical
- Electrical
- Plumbing
- Concrete
- Drywall
- Flooring
- Insulation
- Painting
- Irrigation
Here’s how.
Landscaping
Accurately calculate quantities of landscaping construction elements, plants, trees, shrubs, and other materials needed for your projects.
Additional Read: How to quote with accurate landscaping estimates?
Masonry
Take off quantities of bricks, blocks, stones, and other masonry materials for building walls, facades, and other structural elements.
Mechanical
Accurately estimate the quantities of mechanical systems and components, such as HVAC equipment, ductwork, and piping, required for heating, ventilation, and air conditioning installations.
Electrical
Above all, you can determine the quantities of electrical components, including wires, cables, outlets, switches, and lighting fixtures, necessary for electrical installations.
Paving
You can easily measure the quantities of asphalt, concrete, and other paving materials required for parking lots, driveways, walkways, and other paved surfaces.
Additional read:
How to win paving maintenance and construction bids?
Plumbing
Easily calculate the quantities of plumbing pipes, fittings, fixtures, and other materials required for plumbing systems, such as water supply, drainage, and sewage.
Concrete
Generate automated takeoffs to ascertain the quantities of concrete needed for foundations, slabs, footings, and other concrete structures.
Drywall
You can take off quantities of drywall panels, joint compounds, screws, and other materials needed for interior wall and ceiling installations.
Flooring
Our software helps you estimate the quantities of flooring materials, such as tiles, hardwood, laminate, carpet, and vinyl, required for floor coverings.
Insulation
You can easily calculate the quantities of insulation materials, including batts, rolls, foam boards, and spray foam, needed for thermal and sound insulation.
Irrigation
You can accurately estimate the quantities of irrigation components, such as pipes, valves, sprinklers, and controllers, necessary for efficient water distribution in landscaping construction projects.
Painting
Take off quantities of paint, primers, coatings, and other materials required for interior and exterior painting projects.
By switching to Attentive.ai’s automated blueprint takeoff software, you can streamline the estimating process for a wide range of construction jobs, saving time and ensuring accuracy. Despite having complicated blueprints, you can queue multiple plans and let the software do the heavy lifting.
Along with the legend and an overview of what you need, you can give this detailed takeoff document to a contractor. And they can deliver the end product with no questions asked.
Bonus point- What is a legend? Do estimators use it when getting takeoffs from blueprints?
Another step in doing construction takeoffs from blueprints is using a legend.
The estimator typically checks a legend during the initial stage of reviewing the blueprint takeoffs. In other words, the legend, usually provided within the blueprint or plan documents, contains descriptions and explanations of architectural symbols and notations used in the plan.
There are numerous common symbols there for particular projects. However, symbols’ appearances and meanings can vary, making it crucial for each project to check the legend to ensure an accurate interpretation and understanding of the blueprint.
Switch to automated takeoffs from blueprints
Compared to the manual takeoff technique, turning to automation lowers the possibility of error, reduces waste, and boosts productivity. So that you can win more tenders and run projects more smoothly.
Besides, in today’s competitive construction industry, accurate takeoffs are essential for optimizing bids, staying within budget, and satisfying clients’ expectations. By embracing an automated blueprint takeoff tool like Attentive.ai, contractors and estimating professionals can save time, improve accuracy, and enhance their overall efficiency in the estimation process.
Don’t just take our word for it; try for yourself. In fact, for a personalized demo with Attentive.ai’s team, book a session today.
FAQs
How to do material takeoffs from blueprints?
To do material takeoffs, review the project plans and specifications, identify the quantities of materials needed for each component, and calculate the total amounts required. Hence, for the right estimate, you can rely on Attentive.ai’s automated blueprint takeoffs that are built on 98% accuracy.
What construction document is used for takeoffs?
In general, contractors used to get manual takeoffs tracing physical blueprints that they print out. To do your takeoff accurately, upload the blueprint on Attentive.ai’s automated blueprint takeoff software, define the scope of work, and approve the takeoff.
How do you start a takeoff?
- On the AutoMeasure platform, switch to the blueprint takeoff mode.
- Scan the blueprint into the software for a digital takeoff. Once the layout has been thoroughly examined, the platform creates a detailed list of every material needed for the project.
- In fact, you can make manual revisions as needed.
- The materials can then be given automated, error-free formulas and processed through the software to provide precise construction takeoffs.
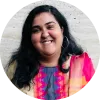