Quality Control Secrets for Busy Landscaping Operations Teams
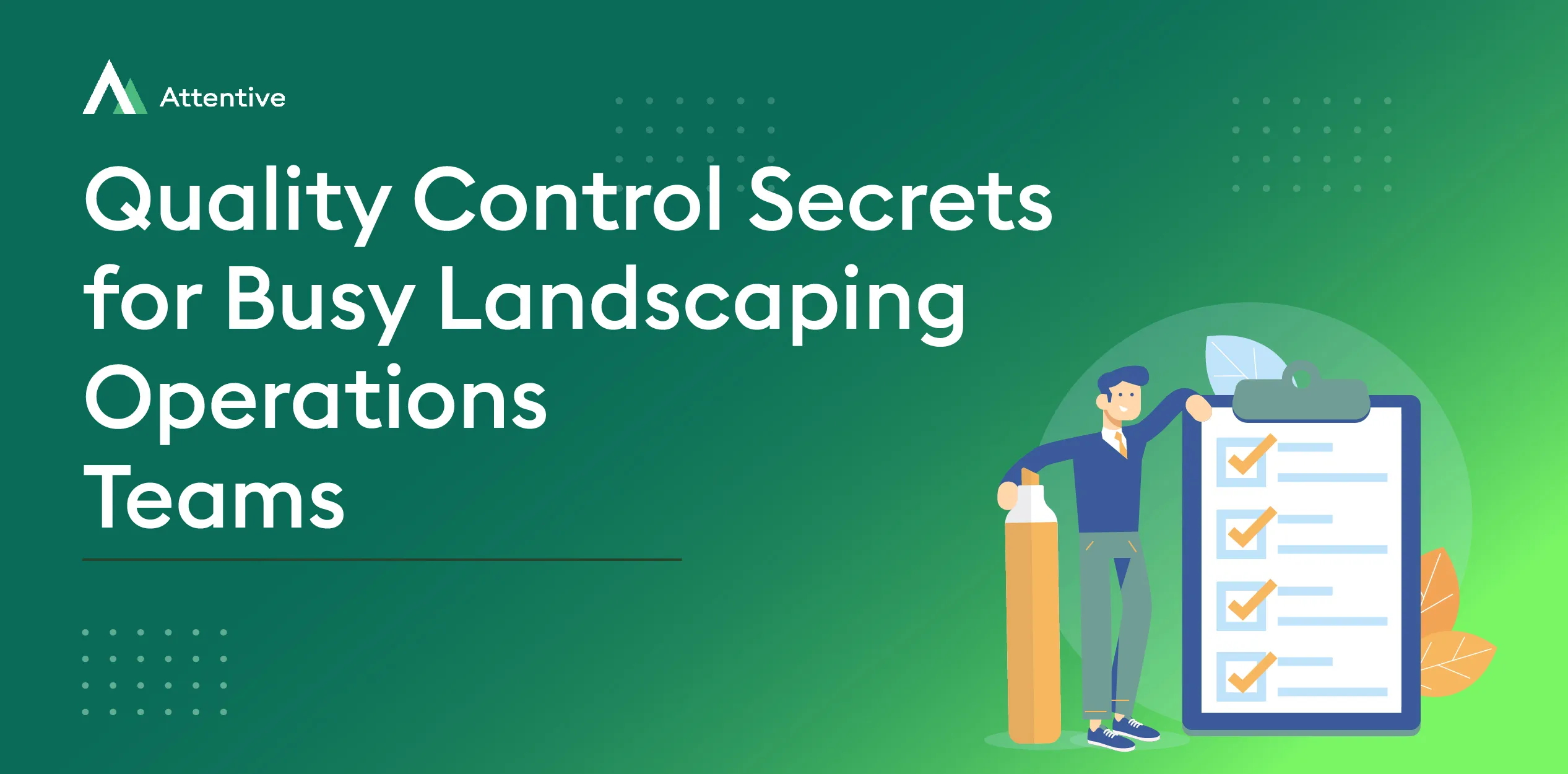
Table of content
Subscribe to get updates from Attentive!
Maintaining high standards in commercial landscaping is essential for your business's success and reputation. And your quality control processes should be straightforward and efficient. Here are some actionable secrets that can help busy landscaping operations teams improve the quality of materials and services, ensuring consistent excellence in every project.
5 Quality Control Secrets for Busy Landscaping Operations Teams
Develop a Comprehensive Supplier Evaluation System
To ensure you’re sourcing the best materials, creating a comprehensive supplier evaluation system is crucial. Here’s a detailed approach:
Regular Quality Assessments
Periodically evaluate the quality of materials provided by your suppliers.
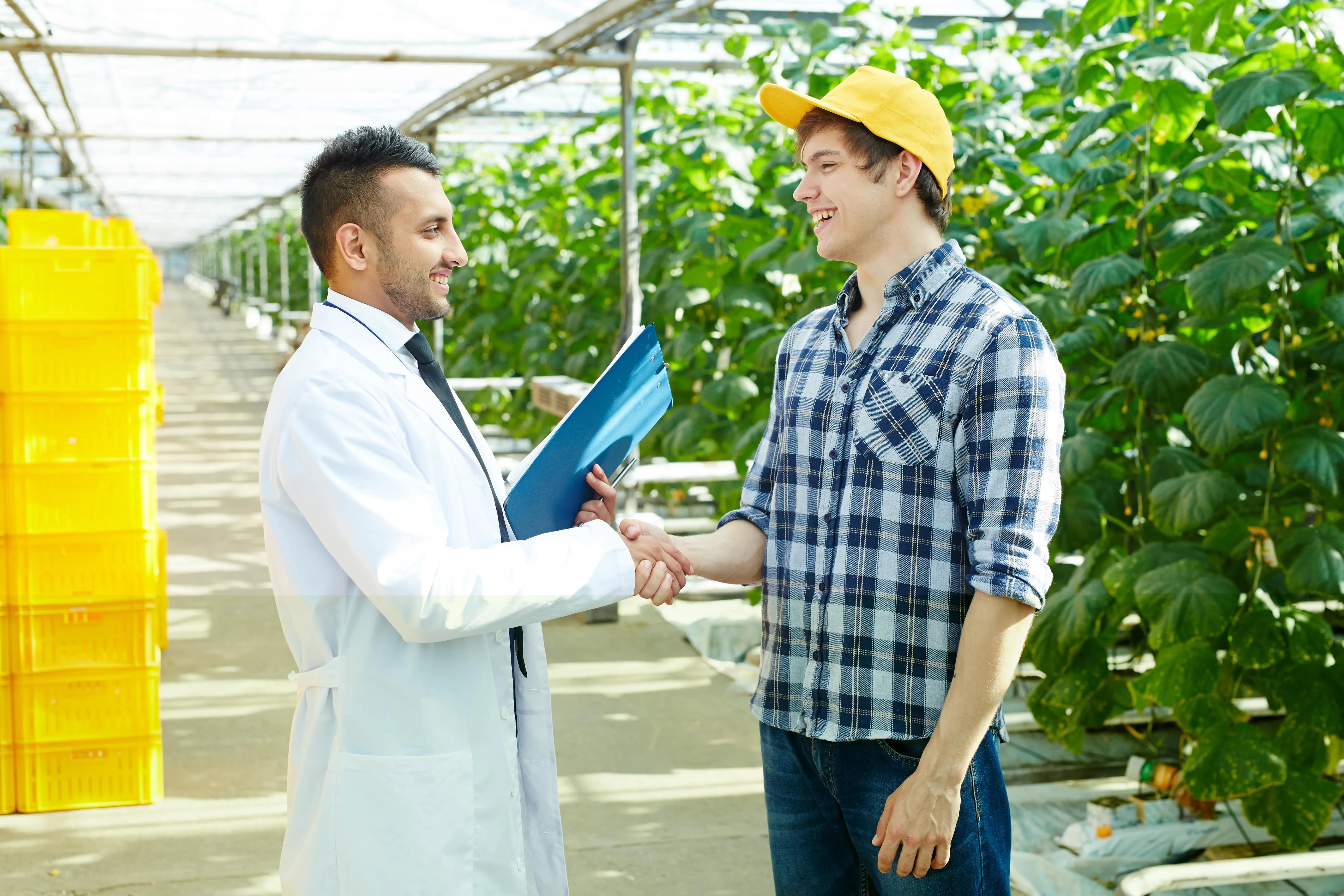
Check for consistency in meeting the specified sizes, specifications, and standards. For example, if a supplier consistently provides 3-gallon shrubs that are robust and healthy, they should score higher.
Price Comparisons and Value Analysis
Regularly compare the prices of materials from different suppliers, taking into account seasonal variations and overall value for money. A supplier offering competitive prices without compromising quality should be rated favorably.
Reliability and Communication
Evaluate the ease of communication with suppliers and their reliability. Are they easy to reach, and do they communicate transparently about delivery times and potential delays?
For instance, a supplier that provides timely updates about shipments and promptly addresses any issues should score higher.
Trustworthiness and Transparency
Assess how much you can trust each vendor. Do they have clear return policies, and are their processes transparent? A supplier with a straightforward and fair return policy should be rated higher.
Now, create a scoring system (e.g., 1-5) for each criterion and review each supplier periodically. For instance, a supplier might score a 4 for quality, a 5 for pricing, a 3 for communication, and a 4 for trustworthiness. Use these scores to make informed sourcing decisions, especially during peak seasons when quick and reliable sourcing is crucial.
Regularly Train Your Team on Quality Standards
Your team plays a crucial role in maintaining quality standards. Regular training sessions can ensure everyone is on the same page:
Standard Operating Procedures (SOPs)
Develop and regularly update SOPs for all common tasks. For instance, have clear guidelines on how to plant trees, install irrigation systems, and handle plant materials.
Quality Checklists
Create checklists for each project phase. For example, a planting checklist might include steps like soil preparation, planting depth, and watering requirements.
Hands-On Training
Conduct regular hands-on training sessions to demonstrate best practices and ensure all team members are familiar with the latest techniques and standards.
Enhance Communication with Nursery Suppliers for Improved Quality Control
Effective communication with nursery suppliers is essential for preventing quality control issues.
Here’s how you can ensure clarity and consistency:
Detailed Specifications
Always provide detailed requirements beyond just the basics. For example, instead of specifying a "3-gallon pot size," include the expected height, fullness, and health of the plant, such as "3-gallon pot with a shrub that’s at least 24 inches tall and fully leafed out."
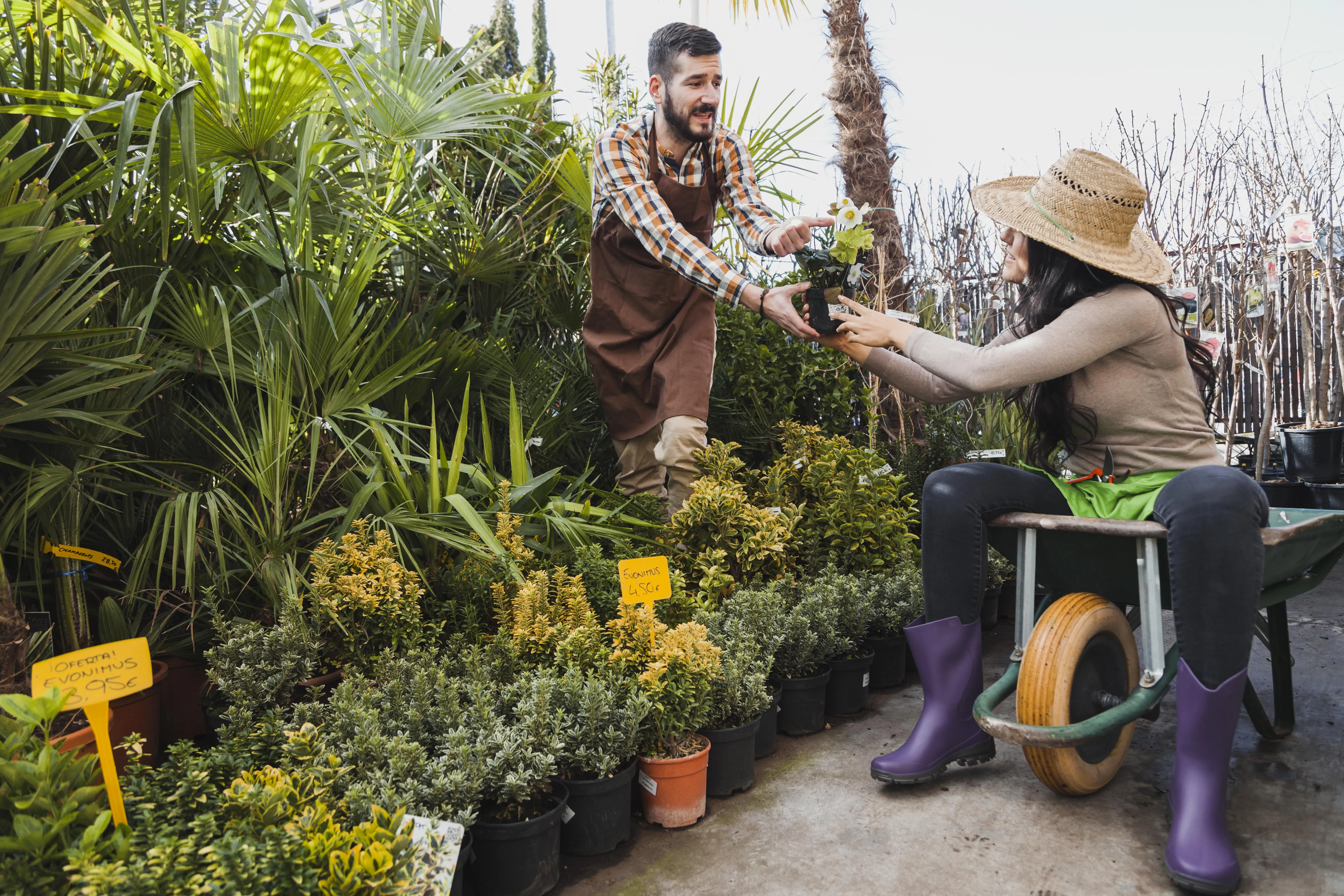
Multiple Confirmations
Confirm the specifications and quality requirements at several stages—during bidding, before confirming the order, and just before delivery. This repetition ensures that both parties are on the same page and reduces the risk of errors.
Utilize Technology for Documentation
Leverage email templates, messaging apps, and project management tools to document all communications. Integrated crew apps also help crew leaders and members document site conditions well. This not only creates a record that can be referred to in case of disputes but also ensures that all details are captured accurately.
Suppose you need a large order of ornamental grasses for a commercial project. You might send an initial email detailing the size, height, and health requirements. Before the order is confirmed, have a follow-up call to reiterate these details and finally, a day before delivery, send a quick message to reconfirm the specifications.
Foster a Culture of Overcommunication Within Your Team
Just as overcommunication with suppliers is crucial, it’s equally important within your team:
Daily Briefings
Hold brief daily meetings to review the day’s tasks, address any concerns, and reinforce quality standards.
Open Communication Channels
Encourage team members to report issues or ask questions without hesitation. Use messaging apps or project management tools to facilitate easy communication.
Feedback Loops
Implement a system for team members to provide feedback on processes and materials. Use this feedback to continuously improve your operations.
Implement Picture-Based Validation for Deliveries
Visual validation is a straightforward yet powerful method to ensure you receive quality materials:
Pre-Delivery Photos
Request your suppliers to send photos of the materials before shipping. For example, ask for images of pallets of sod or batches of shrubs to verify their condition and compliance with your order.
On-Site Inspection and Documentation
Upon delivery, have a designated team member inspect the materials and take photos. Compare these images with the pre-delivery photos to ensure consistency and quality.
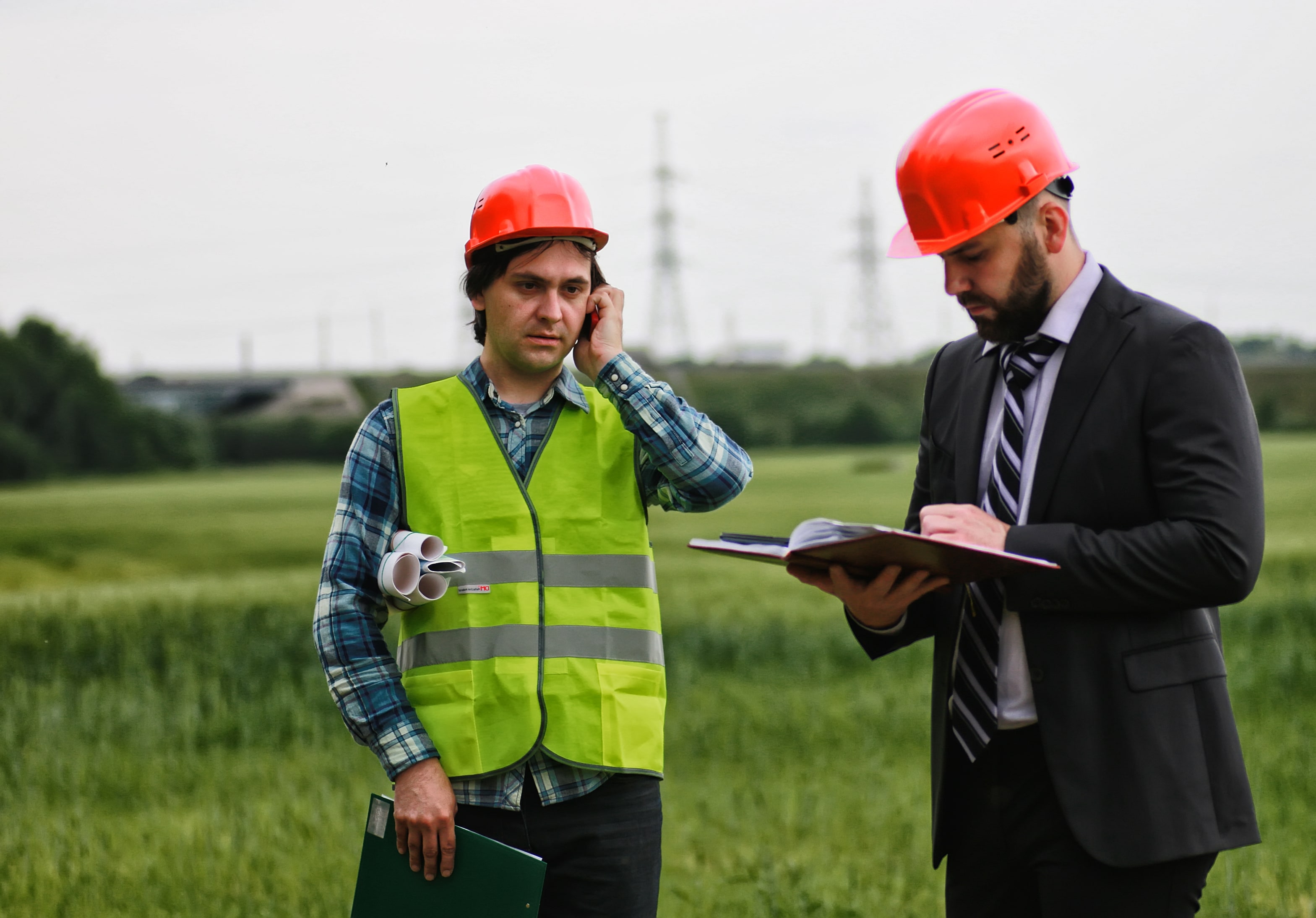
Also read: How To Improve Job Documentation On Sites?
Digital Record Keeping
Use apps or software that facilitate easy sharing and storage of these photos. This creates a visual audit trail that is invaluable for resolving disputes and maintaining quality control records.
If you’re receiving a shipment of trees for a new park project, request the supplier to send photos of the trees from different angles before they are loaded for delivery. Upon arrival, inspect the trees and take your own photos to ensure they match the pre-delivery images.
Monitor and Adjust Based on Feedback
Quality control is an ongoing process that benefits from continuous improvement:
Client Feedback
Regularly solicit feedback from clients about the quality of your services and materials. Use surveys or follow-up calls to gather their input.
Internal Audits
Conduct regular internal audits to assess the effectiveness of your quality control measures. Identify areas for improvement and implement necessary changes.
Benchmarking
Compare your quality standards and practices with industry benchmarks. This can help you stay competitive and ensure you’re meeting or exceeding industry standards.
Over to you
By implementing these quality control secrets, busy landscaping operations teams can ensure consistent quality, avoid delays, and maintain a stellar reputation. Remember, the key is to be proactive, communicate effectively, and continuously seek ways to improve.
For more insights on managing your landscaping business, stay tuned to our blog for industry trends, plant care content, business tips, and more.
FAQs
1. How can a comprehensive supplier evaluation system improve landscaping quality control?
Implementing a rigorous supplier evaluation system ensures that only high-quality materials reach your projects. For example, in regions like Florida where humidity can affect plant health, it's crucial to source from suppliers who provide robust, disease-resistant plants. By regularly assessing supplier performance on criteria like material quality, reliability, and communication, you can maintain high standards and avoid costly project delays.
2. What are some practical tips for enhancing communication with nursery suppliers to ensure quality?
Effective communication is key to ensuring that the plants and materials meet your project's specific needs. For instance, if you're working in urban areas like California where certain plants are preferred for their low water usage, specifying exact requirements such as plant size, type, and drought tolerance ensures suppliers meet your expectations.
3. Why is regular training crucial for maintaining quality standards in landscaping operations?
Regular training ensures that all team members understand and adhere to your company's quality standards. For busy operations teams in Texas, where rapid growth and development can lead to frequent staffing changes, continuous training on SOPs and quality checklists helps maintain uniformity and excellence across all projects. Hands-on training sessions can be particularly effective in teaching proper installation and maintenance techniques for various landscaping elements.
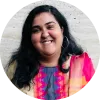